EQUIPMENT
PVD Advanced Technologies Inc. offers a broad range of equipment including PVD, CVD, PACVD, as well as Electron-Beam polishing equipment and sterilizers.
We have the technical expertise to custom design equipment based on client needs; offering full-service solutions for cleaning, coating, post treatments, batch or inline operations.
Electron-Beam Polishing Machine (EBPM-1)
The EBPM-1 is a vacuum DC electron-beam polishing machine, used for surface modification and polishing of ceramics and hard metals. This is achieved by an intensive pulse sub-milisecond electron beam with high density energy, at low accelerating voltage, for a very short pulse duration.
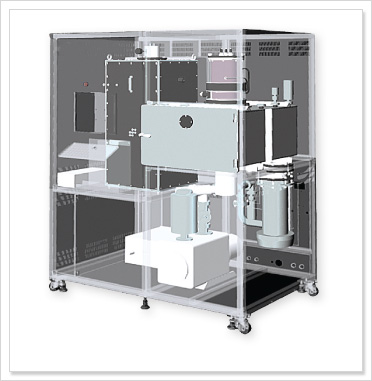
The beam mark is 8cm in diameter on a titanium foil after a single electron-beam shot.
There are not micro defects: cracks and craters. The surface roughness Ra was decreased at 15 times.
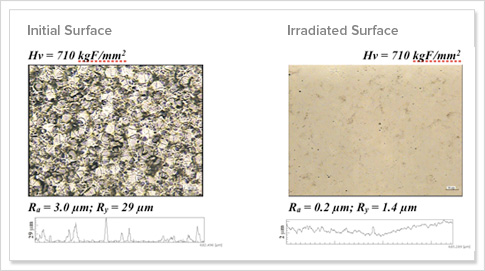
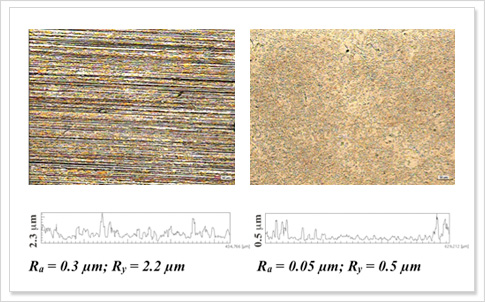
The electron-beam source is integrated into the working chamber equipped with 2D positioning gear.
- Chamber dimensions: (50 × 50 × 20)" or more
- Part-under-treatment dimensions: (24 ×24 ×8)" or more
- Part-under-treatment weight: up to 240lbs
- 2D positioning gear control automatic
- High vacuum pump speed: 1000 – 1500l/sec
- Vacuum: 0.01mBar
- Electron gun
- Gas inlet system
- Pulse power generator based on the energy accumulator, high voltage capacitor and the high-current thyratron
- 35kV DC power supply
- Magnetic filed coils power supply
- Penning discharge power supply
- Multi-channel synchronizing generator
- PC interface controller
- Spare parts including one additional high-current thyratron
Performance
The electron beam parameters are as follows:
- Electron energy: up to 32keV;
- Pulse duration: 3μs;
- Beam current: up to 30kA;
- Beam transportation length: up to 30cm (depending on gun design);
- Beam diameter: up to 9cm (at the beam energy density up to 10J/cm2);
- Beam energy density: up to 20J/cm2 (at the beam diameter below 9cm);
- Beam repetition range: up to 0.2Hz; and
- Working gas (argon) pressure: 0.3 – 1mBar.
The EBPM device is an electron-beam source based on the plasma-filled diode generating the high-current electron-beam and providing transportation of the above-mentioned beam. The block diagram of the electron beam gun is shown below. After vacuuming down to 10 – 6mBar, the chamber is filled with high-clean argon at a pressure of 10 – 4mBar to 10 – 3mBar. A voltage pulse amplitude of a 30kV is applied. This action ignites pulsed reflective discharge. This is followed by the application of the main voltage, after the time delay required by the plasma to fill the whole working space.
The increase in voltage forms the cathode sheath, where electric field strength exceeds the cathode surface breakdown strength, and the cathode gets covered with dense explosive-emission plasma.
A rapidly-moving bi-layer is formed between anode and cathode plasma due to variation in plasma densities, which provides electron acceleration in a rather thin gap while bi-layer passes between the cathode and the anode. A thin acceleration gap in conjunction with compensation of electron space charge, due to background anode plasma allows production of dense electron-beams of a few microseconds duration at low accelerating voltages.
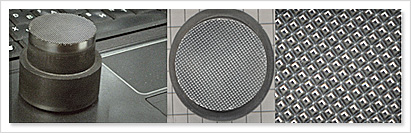
Effects
- High quality polishing
- No micro defects as cracks and craters
- The surface roughness Ra was decreased at 15 times.
Electron-Beam Polishing Machine AC (EBPM-2)
The EBPM-2 is a vacuum pulse electron-beam polishing equipment used for the surface modification and polishing of ceramics and hard metals.
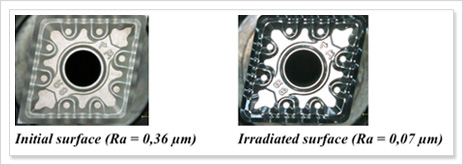
This is achieved by intensive pulse sub-milisecond electron beam with high density energy at low accelerating voltage for very short pulse duration.
Equipment Properties
- Dimensions of the unit: (1350 x 2150 x 200)mm
- Dimensions of the vacuum chamber: (600 x 500 x 400)mm or more
- Voltage: 5 – 25keV
- E-beam current pulse duration: 20 – 200μs
- Impulse frequency: 0.3 – 20Hz
- Electron energy density: up to 100J/cm2
- Maximum power consumption, depending on the accelerating voltage source used: 2.5 – 10kW
- Working pressure: 0.01 – 0.05Pa
- Working gas: Ar
- Imprint diameter (surface melting zone diameter without scanning mode): 2 – 5cm
- The dimensions of the manipulator scanning region: (400 x 400)mm or more
- Water flow limit for cooling: not more than 0.4m3/h
- Independent smooth control of main parameters: beam current, average energy of electrons, pulse duration, pulse repetition range
- All units and devices have electron-beam parameters preset and controlled by software in the treatment process.
Electron Beam Treatment
- Surface melting
- Evaporation
- Structure modification
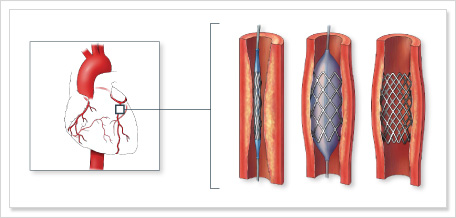
Effects
- Surface planning
- Crystal structure modification
- Surface polishing
NANO-ARC (1000 and 650)

The Nano-Arc 1000 combines plasma ion-assisted and plasma arc-deposition technologies to create functional surfaces under high energies and particles for implantation in a nano-chrystalic and multi-layered form. Our vaccum machines are equipped with plasma-generators, non-self-arc-discharge, low-pressure plasma-ion, to perform nitration, final cleaning and surface activation.
The deposition is done by using plasma assisting technology in a vacuum electric-arc deposition. Plasma technologies combine several components generating extremely hard functional surfaces, various chemical elements and their combinations, in a single vacuum cycle.
Vacuum combined plasma-ion assisted and plasma-arc-deposition creates functional surfaces under high energies and particles for implantation in a nano-chrystalic form, extremely hard and multi-layered. The coatings achieved through this technology have enhanced properties for: heat, corrosion and erosion resistance.
Our technologies and vacuum equipment are best for applying multi-components of various chemical elements and their combinations. Due to the nano-structure of the coating, the wear resistance and corrosion protection increase dramatically. The unique magnetic system of the planar arc evaporator allows for a uniform coating composition and thickness with very high performance. The maximum surface roughness of the coating is 0,04Ra.
Our coatings perform best in high wear and high corrosion conditions.
Applications
- Turbine blades
- Engine and machinery components
- Cutting tools
- Stamping tools
- Molds and dies
- Surgical blades
Nano-Arc-1000
- Big size high speed PVD coating machine
- Application: forming and cutting tools
- Chamber O.D.: (850 x 1000H x 1200)mm
- Plasma zone and layout designed for forming and cutting tools: up to 1000kg
- Typical coating temperature: 3000-4500C
- Four (750 x 80)mm planar or cylindrical arc evaporators with mechanical shators (options: 4 planar or cylindrical magnetrons or 2 magnetrons and 2-arc evaporators)
- One plasma generator (nitrating, heating, cleaning, plasma-assisted process)
- Two heaters 24 kWt
- TMP (2 x 2000 l/s) + mechanical pumps
- PLC + PC control system
- Process time: coating 0.5 – 1 hour, pumping chamber 3 – 4 hours, coating speed 10 – 15 microns/hour with rotation parts
- Coating process: low heating, plasma heating, cleaning, plasma stripping old coating, nitrating, sputtering 4 metals or nitriding and carbonitriding, TiN, TiCN, TiAlN, CrN , ZrN, (TiAlMoZr)N
- Coating 4 metals simultaneously
Nano-Arc-650
- Small size high speed PVD coating machine
- Application: forming and cutting tools
- Plasma zone and layout designed for forming and cutting tools up to 500 kg
- Typical coating temperature: 2000-4500C
- Chamber O.D.: (650 x H650 x 700)mm
- Four (400mm x 80)mm planar or cylindrical arc evaporators with mechanical shatters (options: 4 planar or cylindrical magnetrons or 2 magnetrons and 2 arc evaporators)
- One plasma generator (nitriding, heating, cleaning, plasma-assisted process)
- Two heaters 6 x 2kWt
- One TMP (2000 l/s) + mechanical pumps
- PLC + PC control system
- Process time: coating 0.5 – 1 hour, pumping chamber 2 – 3 hours, coating speed 10 – 15 microns/hour with rotation parts
- Coating process: low heating, plasma heating, cleaning, plasma stripping old coating, nitriding , sputtering 4 metals or nitriding and carbonitriding, TiN, TiCN, TiAlN, CrN
- Coating 4 metals simultaneously
Equipment Properties
- Dimension of vacuum camera: diameter 950mm, height 1200mm – 1500mm
- Operating vacuum (Pa): -10-³
- Plasma zone and layout designed for forming and cutting tools: up to 1000 kg, 750mm x 800mm
- Typical coating temperature: 1500C – 3500C
- Four planar or cylindrical arc evaporators with shatters, 800mm x 80mm
- Plasma generator (nitriding, heating, cleaning, polishing, plasma assistance process), 900mm x 120mm
- Two heaters: 24kWt
- One TMP: 2000 x 2l/sec
- PLC+PC control system
- Area taken by the equipment: up to 20mm²
- Height of the equipment: 2.5m
- Weight of the equipment: 2500kg – 3000kg
- Electricity used: up to 60W
- Water used: up to 2.0m³/h
- Linear dimensions for parts that are being worked on: 750×800
- Surface that can be worked on: up to 6000cm²
- Time for one working cycle: 60min
- Process: plasma heating, cleaning, polishing, plasma stripping old coating, nitriting, TiN, TiCN, TiAlN,CrN etc.
ElectraPulse 200
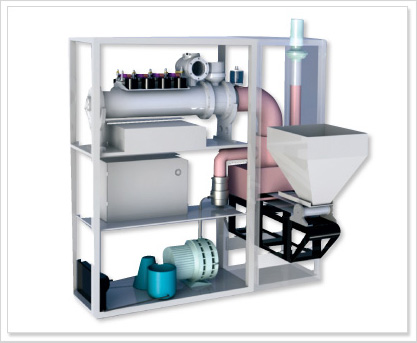
Electrapulse 200 is an electron-beam sterilizer which combines high energy field with very short pulse duration and has the ability to dry sterilize a wide range of products.
Mechanism of Sterilization
- Air Plasma (ozone, oxygen radical)
- Short-pulsed high energy electrical field
- Alpha and Gamma radiation
Advantages
- The object is fully free of induced radioactivity
- Very short treatment time: 0.6 – 3 seconds
- It does not increase the temperature of the treated object
- Low power consumption
- No capital radiation shielding
- Compact setup
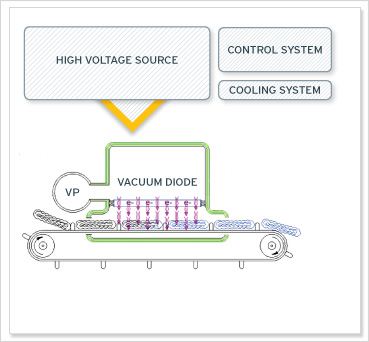
Equipment
- Energy of electrons: 230 – 250keV
- Pulse current: 5 – .5kA
- Current pulse duration (FWHM): about 7 – 10ns
- Area of e-beam cross-section: 7.5 x 25cm (about 200cm2)
- Pulse repetition frequency (adjustable): 1 – 100Hz
- Operation mode: continuous long time or batch
- Power net: 3 x 400V, 50(60)Hz, 4kW